Dual-Range Force Sensor (DFS-BTA)
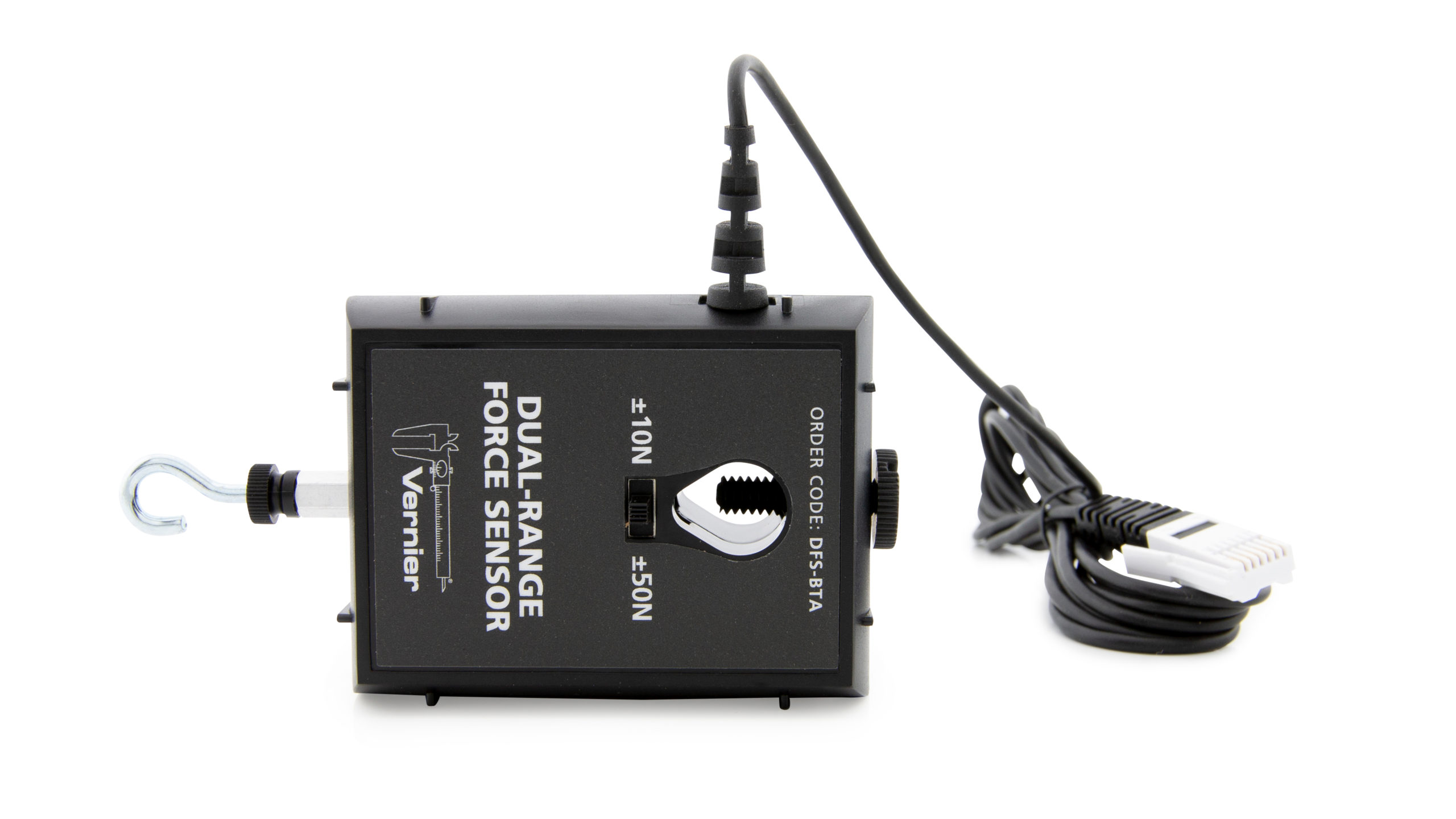
Troubleshooting
- Primary Test: Does the sensor read near zero when no force is applied? Does the sensor read a positive value when pulling, and a negative value when pushing?
- Secondary Test: Point the hook downward. With nothing attached, note the reading. Then hang a 500 g mass from the hook and note the new reading. Is the difference approximately 4.9 N?
- Additional Tips
- Confirm that the switch setting on the sensor is appropriate for the experiment. In general, you should use the +/-10 N range if you can. If the forces exceed 10 newtons, use the +/-50 N range.
- Was the sensor properly zeroed? If you plan to use the Dual-Range Force Sensor in a different orientation (horizontal vs. vertical) than it was calibrated, zero the force sensor in the orientation in which you want to use it. This additional step makes the sensor read exactly zero when no force is applied.
Additional Troubleshooting
- How do I put the Vernier Dynamics System mass and the dual range force sensor on the green metal dynamics cart at the same time?
- What is the best way to arrange the Dual-Range Force Sensor and Pasco masses on the same dynamics cart?
- How can I change the sign of the force reading? (Make either push or pull positive or negative)
- Dual Range Force Sensor does not respond to a push, but does measure a pull.
- Can your force sensors be used in a test section of a wind tunnel for educational demonstrations?
- What is the difference between the Dual Range Force Sensor and the Student Force Sensor?
- My Dual-Range Force Sensor is noisy when used with a Motion Detector and LabPro.
- Why does my data table have holes (empty cells) in it?
- Problems with force sensor giving bad readings because hex barrel has been removed and improperly reinstalled.
- What replacement parts are available for the Force Sensor?
- How can I make my own hoop bumper to use with a Vernier force sensor?
- My force sensor fell into the floor, and now the hex bolt sheared off inside the load cell.
- Can the cable on a Dual Range Force Sensor be repaired?
Specifications
- Resolution
±10 N Range: 0.01 N
±50 N Range: 0.05 N
Calibration
Calibrate? No. The sensor is set to the stored calibration before shipping.
If you wish to calibrate the sensor, you will need to conduct a two-point calibration. For calibration using the ±10 N range, use a 300 grams of mass (2.94 newtons). For calibration using the ±50 N range, use a one kilogram mass (9.8 newtons).
- First point
⚬ Remove all force from the sensor.
⚬ Enter 0 as the first known force. - Second point
⚬ Hang a mass from the force sensor hook.
⚬ Enter the weight of the mass. (Note: 1 kg applies a force of 9.8 newtons).
⚬ Do not exceed the selected range setting during calibration. - Zero the force sensor in the orientation you will be using it.
If you wish to store a calibration to the sensor, see How do I store the calibration for my sensor using Logger Pro?
Related Products
- Dual-Range Force Sensor Replacement Parts Kit (DFS-RPK)
- Bumper and Launcher Kit (BLK)
- Hoop Bumpers for Bumper and Launcher Kit (HOOPS-BLK)
- Magnetic Bumpers (MG-BMPRS)
- Clay-Holder Bumpers with Clay (CLAY-BMPRS)
- Air Track Adapter (ATA-DFS)
- Force Table Adapter (FTA-DFS)
- Adapter for PASCO Cart (PCA-DFS)
- Springs Set (SPRINGS)
- Go Direct® Force and Acceleration Sensor (GDX-FOR)